Wednesday, April 30, 2014
How to Replace a 2003 Ford Focus PZEV 2 3L Air Filter

The air filter in the 2003 Ford Focus PZEV 2.3L is different from a standard filter. A standard filter is a small paper cartridge that is placed inside an air filter assembly. The Focus PZEV -- which stands for "partial zero emissions vehicle" -- uses an air filter box with a special nonserviceable foam element inside. In order to replace this filter, you have to replace the entire box, which is fairly expensive. But you should only have to replace the filter every 150,000 miles.
Instructions
- 1
Lift the hood of the Focus and prop it open.
2Locate the air filter box. It is the large black box just behind the left headlight.
3Unbolt the air filter box from the air intake hose using the socket wrench and socket.
4Remove the air filter box from the engine bay and place the new one in its place.
5Connect the new air filter box to the air intake hose and bolt it into place.
How to Jump Start a Saturn Vue

Extremely cold outside temperatures or leaving the lights on while the motor is off, are factors that may cause the battery in a Saturn Vue to lose its charge. In the event that this happens, you will need to perform a jump start to get the Vue up and running. Exercise caution when performing a jump start because there is a risk, albeit remote, that an explosion may occur.
Instructions
- 1
Open the Saturn Vues hood and locate the terminals on the battery.
2Move the operational vehicle close enough to the Vue that the jumper cables can reach between them.
3Connect one of the jumper cables red clamps to the positive (+) terminal on the dead battery, and then connect the other red clamp to the positive terminal on the jumper vehicles battery.
4On the jumper vehicles battery, connect a black clamp to the negative (-) terminal and then connect the other black clamp to an unpainted metal surface on the engine block to ground the connection.
5After five to 10 minutes, start the Saturn Vue. Idle the engine for another five to 10 minutes before disconnecting the jumper cables.
6Disconnect the jumper cables by reversing the above steps. Close the hood. The jump start process is now complete.
Tuesday, April 29, 2014
How to Reset the Service Engine Soon Light on a 1997 Saturn L1

You can reset and turn off the "Service Engine Soon" light on your 1997 Saturn L1. The On-Board Diagnostics computer keeps track of regular service intervals. Its important to always do the servicing first before resetting the light. This will allow the vehicles computer to keep accurate track of when the next service is due.
Instructions
- 1
Pop open the hood of the vehicle. Find the battery. Behind the batter is a black fuse box. Release the retaining clips and lift off the top of the box.
2Look for the "Reset" button below a reddish-orange block. Press the button and hold it for five seconds.
3Put the key in the ignition and turn the vehicle on, but dont start the engine. Wait one minute. The light should have turned off. If not, turn off the vehicle and turn the ignition to the "ACC" setting. Press the "Reset" button again and hold it for 15 seconds.
4Turn off the car and remove the key. Put the key back in the ignition and start the engine. Let it run for at least two minutes. The computer should now have registered the reset and the service engine light should now be off.
How to Repair a Defroster
The rear-window defroster on your vehicle uses an electric current to keep the view free of condensation, frost and ice. Scratches in the conductive paint and broken defroster tabs are common reasons for defroster failure. The materials required to fix both problems are readily available and inexpensive. A successful repair of the defroster requires proper preparation.
Instructions
- 1
Spray window cleaner on the rear window of the vehicle and wipe the window with a rag or newspaper. Inspect the defroster tab. Crack the vial contained in the defroster repair kit. Apply the adhesive in the vial to the window and the back of the defroster tab supplied with the repair kit. Hold the defroster tab against the window for one minute. Slide the connector for the defroster onto the repaired tab.
2Start the vehicle. Turn on the rear defroster.
3Place the black and red leads of a voltmeter on each defroster grid. When the voltmeter reads zero, you have found the broken lead.
4Apply the masking tape supplied with the defroster repair kit above and below the broken line in the defroster grid. Shake the container of conductive paint for 30 seconds.
5Spray the conductive paint over the gap left between the top and bottom sections of masking tape. Remove the masking tape from the window. Allow the paint to dry for 30 minutes before using the vehicles rear-window defroster.
Monday, April 28, 2014
How to Replace the Evaporator Core in a 2003 Dodge B250 Van
The evaporator core, or heater core in a 2003 Dodge van is a radiator that contains hot coolant. The coolant circulates through the heater core when the heater is turned on, warming the interior of the van.
Instructions
- 1
Remove the negative battery cable with a socket wrench, and wait two minutes. This allows the capacitor in the airbag system to discharge, and prevents the airbag from deploying. Discharge the rigerant in the air conditioning system, and detach evaporators suction line jumper.
2Remove the mounting screws that attach the heater to the air conditioning unit with a socket wrench. Push the mounting bracket and rigerant lines out of the way to gain access to the heater.
3Detach the wiring harnesses for the fin sensing cycling clutch switch, blower motor resistor and blower motor relay. Cover the alternator with a shop cloth to prevent coolant from spilling on it. Drain the coolant in the radiator into a clean container for later use.
4Disconnect the coolant hoses from the heater with a socket wrench. Remove the right headlight assembly, support assembly for the right radiator core, support panel for the right cowl grille and the grille panel. Disconnect the screws that attach the heater housing to the blower motor housing.
5Disconnect the door motor link from the distribution duct in the passenger compartment. Use a socket wrench to remove the nuts in the glove compartment that fasten the heater to the dashboard.
6Remove the stamped nut in the engine compartment that connects the heater housing to the dashboard with a socket wrench. Detach the heater housing from the housing for the blower motor. Pull the heater housing from the dashboard so that the door link clears the hole in the dash panel. Remove the heater housing from the vehicle.
7Remove the pivot shaft nut from the blend-air door of the heater housing with a socket wrench. Pivot shaft nut. Detach the mounting flange boot and lever from the blend-air door. Disconnect the motor relay and its mounting bracket from the high-speed blower motor on the heater housing. Disconnect the screws from the top cover of the heater housing with a socket wrench, and remove the cover.
8Remove the screw that fastens the tube support bracket for the heater core to the mounting boss. Remove the heater core from its housing.
9Place the new heater core into its housing, and fasten its support bracket to the mounting boss with the retaining screw. Tighten the screw to 20 inch-pounds with a torque wrench.
10Complete the installation of the new heater core by performing steps two through seven in reverse order. Attach the suction line jumper for the evaporator, and charge the air conditioner with rigerant. Connect the cable for the negative battery terminal with a socket wrench.
DIY Car Amp Repair

There are a variety of reasons why a car audio amplifier might malfunction, most of which render the amplifier useless until it has been fixed. Most car amplifiers are fitted with a function that completely shuts the amp down if there isnt a complete circuit connected to the amplifier, but it may not help you fully diagnose the problem. Most problems lie within the wires themselves, so making sure theyre repaired and working properly is key.
Instructions
- 1
Find the red wire on the left side of the amplifier. Connect one end of the voltmeter to this wire and the other end to a piece of exposed metal. This should make a complete circuit. If the amplifier does not power on following this, then the problem may be with the amplifiers wiring.
2Find the ground wire at the back of the amplifier. The wire is black and should be attached to a piece of exposed metal. Apply a piece of electrical tape to the ground wire and attach it firmly to a piece of exposed metal if not already connected. This creates a full circuit.
3Remove the white fuse from the fuse terminal located on the left of most amplifiers and replace it with a new one. A blown fuse will generate no power for the amplifier, rendering it useless.
4Stick pieces of electrical tape to each wire that is coming out and into the back of the amplifier. Each wire is partially exposed at one section to allow a connection to the fuse terminal. However, this can cause short circuits, and the connection between these wires and the fuse terminal isnt vital as it is powered by the main wire running on the side of the amplifier.
Sunday, April 27, 2014
How to Change a Choke Cable on a Harley

Harley-Davidson always calls its choke cable the "enrichener." Pulling the enrichener knob out increases the percentage of fuel in the carburetors fuel/air mixture, which helps cold engines start. Pushing the knob in returns the fuel/air mixture to normal levels. This is a small and inexpensive component, but many riders hesitate to replace the enrichener themselves because written instructions for the procedure are non-existent. Replacing the cable assembly requires at least the partial removal of the carburetor. You can remove the carburetor completely, but if you leave the carburetor loosely attached to the intake manifold, the throttle cables and fuel line remain intact.
Instructions
- 1
Empty the carburetor of fuel by closing the petcock and starting the engine. Let the engine run until it stalls.
2Remove the entire air cleaner assembly, including the air cleaner cover, the air cleaner and the air cleaner backing plate. Use an Allen wrench to remove the cover, Torx sockets or drivers to remove the air cleaner and a socket wrench to remove the backing plate. Disconnect the breather tubes by hand.
3Detach the enrichener knob from the bracket above the horn.
4Pull the carburetor partly out of the black, rubber seal ring that connects it to the intake manifold. Use a flashlight or shop light to locate the enrichener cable and find where it screws into the carburetor. Remove the old cable by unscrewing it.
5Clip the knob end of the new enrichener assembly into the bracket above the horn. Snake the enrichener valve end of the new enrichener cable assembly under the gas tank to the back of the carburetor.
6Insert the wire and ball end of the enrichener valve into the opening in the back of the carburetor. Thread and hand-tighten the black, plastic cable sealing cap on the end of the enrichener assembly to the back of the carburetor. Do not use a wrench.
7Reseat the carburetor in the seal ring. Visually inspect the carburetor. Reattach the entire air cleaner assembly, including the breather tubes.
Help Needed With a Paintless Dent Repair

Paintless dent repair (PDR) is the removal of dings and dents from a motor vehicle body through different techniques. The techniques used in paintless dent repair do not require painting after the dent is corrected. If the paint was damaged at the time the dent occurred, paintless dent repair is not possible. The dent can still be corrected, but a paint job will be required to finish the repair. This is known as "push to paint". Paintless dent repair is often used to correct dents caused by minor damages such as hail damage and door dings.
Instructions
- 1
Remove a small dent with a the use of glue and a dent pulling tab. Several companies sell paintless dent repair kits which include a hot glue gun with glue sticks and a dent pulling tab with accessories. Buy a kit online or through your local auto supply store. Glue a dent pulling tab to the center crease of the dent. Suction the bridge to the car over the dent so that that the dent pulling tab connects through the center of the bridge. Screw the turning knob onto the other end of the pulling tab. Continue twisting the knob, slowly, until the dent pops out. Remove any glue that sticks to the car with rubbing alcohol.
2Wrap a small brick of dry ice in a shop towel and gently apply it to hail damage. Slowly rub over and around the dent for several minutes until the dent pops out. This process can take awhile and is not recommended for dents larger then the size of a quarter. Wear protective gloves while handling the dry ice as it can burn your skin. Leave the vehicle in the shade or a cooled garage for at least half the day once you have removed the dent. Taking the car out into the sun or heat too quickly can cause the dent to return.
3Contact a local PDR company to have your dent removed if you have a medium to large dent. For dents this size, you will only have one chance to get it right and will need a professional to ensure it is done right.
4Attend a short course on professional paintless dent repair. Institutes such as Superior Auto Institute and M & M Training offer courses which can be completed in a few weeks. You will get plenty of hands on experience as well as access to some of the best dent removal tools available. The information offered through these courses will give you an understanding of the different types of dents as well as techniques to remove them.
5Obtain a professional dent removal kit and begin practicing. Kits can be bought through online retailers and training facilities. Make sure the kit comes with a door set, a pry set and wire set. You will also need a ball peen hammer and a rubber tipped crowning tool, a window wedge and a tool leverage strap.
6Buy a fluorescent light that will project shadows onto the surface of a car. The lines and shadows created by the light can be used to gain better insight into the contour of the dent and whether there are any points that are crowning or pressurized. This tool is imperative in successfully and professionally completing a PDR.
7Ask a local salvage yard if you can practice removing dents on their cars or find yourself a practice car and practice if you plan to use your knowledge of PDR for business.
Saturday, April 26, 2014
How to Fix the Reverse Lights to a 1996 Jetta
Blown reverse light bulbs are the most common reason that your 1996 Volkswagen Jettas reverse lights will not illuminate. At its core, however, the reverse light system is controlled by a simple two-wire switch, called a reverse or back-up switch, attached to the transmission. When the switch fails, it will prevent the lights from illuminating at all. Removing and replacing the reverse switch, while outwardly simple, requires removal of the battery box and air box to provide enough clearance for your tools.
Instructions
- 1
Park the Jetta and set the parking brake. Let the engine cool for at least one hour.
2Open the hood and support it in an raised position, using the hood support rod.
3Unclip and remove the battery box cover. Disconnect the cables from the battery, starting with the negative cable followed by the positive cable, using a combination wrench. Remove the battery retaining strap using a ratchet. Lift the fuse box off of the battery, then pull the battery out of the battery box. Unbolt the battery box from the engine compartment using a ratchet.
4Squeeze the spring clamp attaching the air box to the intake duct using pliers. Move the clamp away from the air box. Unclip and remove the air box cover, then pull the air filter out of the air box. Unbolt the lower half of the air box using a ratchet. Pull the air box out of the intake tube, then lift it out of the engine compartment.
5Look between the right side of the transmission housing and the inner engine compartment wall, directly below the air box mounting point. The reverse switch is located directly below the upside-down L-shaped shift linkage at the top of the transmission housing. Alternatively, the reverse switch is located on the top right side of the transmission housing, if you are working on a Jetta fitted with an automatic transmission.
6Unplug the two-pin electrical connector at the rear of the reverse switch. Unscrew the reverse switch from the transmission using an adjustable wrench.
7Screw the new reverse switch into the transmission housing by hand. Tighten the switch to 15 foot-pounds, using a crow foot wrench and a torque wrench. Plug the electrical connector into the end of the switch.
8Push the air box into the intake tube, then slide the spring clamp into place. Reinstall the lower air box into the engine compartment, followed by the air filter and air box cover.
9Reinstall the battery box and battery. Place the fuse box over the top of the battery, then reattach the battery cables, starting with the positive cable followed by the negative cable. Tighten the battery terminal bolts using a combination wrench.
10Reattach the battery box lid and close the Jettas hood.
What Does OEM Car Parts Mean
Original equipment manufacturer car parts are identical to the parts installed in cars at the time theyre built. OEM is a term used when erring to these types of car parts.
Description
Most automobile makers do not manufacture the car parts used in the production of the vehicles they build. Hired manufacturing companies are used for this purpose.
Process
The OEM company builds the parts and puts them in boxes with the car manufacturers name on them. Customers may theore believe they are buying a part directly built by the car manufacturer.
Features
After a specified period of time, varying by manufacturer, the car parts manufactured by OEMs no longer are placed in boxes with the car manufacturers name. At this time, the parts are placed in boxes with only the OEM companys name on it. The parts are identical, but cost less because the brand name is no longer on the package.
Friday, April 25, 2014
1992 Chevy Silverado 4X4 Troubleshooting

The 1992 Chevy Silverado 4x4 is a pickup truck that allows users to haul or tow heavy trailers or loads. If you are having problems with your 1992 Chevy Silverado, you will need an OBD (on-board diagnostic) machine to check the engine. Gaining access to an OBD machine will require you to rent one from a body shop or auto repair center. After you get the troubleshooting code from the OBD scan tool, you will be able to fix your Silverado.
Instructions
- 1
Look in the footwell of the drivers side of the truck for the 16-pin plug. This runs off of the main wiring harness on the left of the fuse panel.
2Plug the OBD cord into the plug. Turn on the OBD machine and then turn on the ignition in the truck so that the electrical panel comes on.
3Press the "Start" button on your scan tool and then wait for the machine to send you a troubleshooting code.
4Unplug the OBD pin from the truck and then turn the truck off.
5Compare the code against the code explanation in your ODB erence manual to find out the problem with the engine. The erence manual comes with the machine rental. It allows you to look up the troubleshooting code for the specific reason your truck is not working properly.
How to Replace a Taillight on a Pontiac Montana
Replacing a taillight bulb in your Pontiac Montana will only take you a few minutes. It is a simple project yet critically important. If the taillight bulbs are not functioning, traffic behind you will not know when you are stopping or turning, causing an unsafe situation that may cause an accident. The 3057 bulbs used in the Montana taillights are readily available at any auto parts stores and are often sold in pairs just in case you need two.
Instructions
- 1
Open the rear lift gate on your Montana and locate the three screws along the top and side of the taillight assembly. The screws are Torx head, and are tucked between the plastic taillight and the rubber seal around the lift gate opening.
2Remove the three Torx head screws with a Torx head screwdriver and set them aside. Grasp the taillight assembly on the sides and pull it straight back, away from the body. Turn the assembly so that the lens is facing down and locate the bulb holder on the rear. Remove the holder by pressing the four locking tabs on the holder.
3Separate the bulb holder and the assembly, setting the assembly aside. Locate the defective bulb, grasp it by the bulb top, and pull it out of the holder. Discard the old bulb and replace it with a new 3057 bulb by pushing the bulb into the bulb holder until it seats.
4Position the bulb holder on the rear of the taillight assembly and snap it in to place, ensuring that all four tabs engage properly. Position the taillight assembly on the van and install the retaining screws along the inboard edge of the assembly. Tighten them with a Torx screwdriver.
5Move to the opposite side of the van and repeat the process if the opposite light has a bulb out. Close the lift gate and test the lights by turning the headlight switch on or stepping on the brake pedal.
Thursday, April 24, 2014
Rebuilt Alternator Problems

When a car breaks down, the cost to replace a failed part, coupled with the labor, can be staggering. Often, there is a choice between a newly built or rebuilt part, especially for vehicle parts like the alternator.
Identification
An alternator is the electrical support of the cars engine. It supplies a charge to the car battery, as well as all the electrical needs of the vehicle, such as powering the headlights. A rebuilt alternator is usually cheaper than a new one.
Considerations
Problems with a rebuilt alternator can mimic those of a new alternator. Bearings can be improperly installed upon rebuilding or wiring can be either attached incorrectly or poorly soldered for a loose connection. Also, rebuilt alternators can be installed by the mechanic incorrectly, which can cause electrical issues in the vehicle.
Significance
Often, consumers do not feel comfortable with a rebuilt alternator, though it can cost 25 to 40 percent less than new alternators. Keep in mind that rebuilders want to sell these parts, so quality assurance is of utmost importance. Its a good idea to see what warranties are available for parts and labor of a rebuilt alternator.
Signs That a Catalytic Converter Is Going Bad
A catalytic converter is an exhaust emissions device that is part of a vehicles exhaust system. In charge of lowering the exhaust emissions that exit a vehicles tail pipe, a catalytic converter can negatively impact vehicle performance if it goes bad or stops working properly. What follows is a brief list of the most common signs of a bad catalytic converter.
Reduced Exhaust Flow
A major sign of a plugged up and/or bad catalytic converter is reduced exhaust flow measured at the vehicle tail pipe. Engine exhaust must travel through a catalytic converter before exiting the tail pipe; a bad catalytic converter can block and/or impede exhaust flow.
Reduced Engine Power
If a bad catalytic converter seriously impedes the flow of a vehicles engine exhaust flow, reduced engine horsepower can occur. This is due to the increase in engine exhaust back pressure that results whenever engine exhaust flow is impeded and/or reduced.
Reduced Exhaust Pipe Temperature
It is common for a bad and/or plugged catalytic converter to cause abnormally low exhaust pipe temperatures on the backside of a catalytic converter. As engine exhaust exits an engine and travels down the exhaust system and through the catalytic converter, the exiting exhaust flow can be restricted enough to cause significantly reduced exhaust pipe temperatures between the catalytic converter and the tail pipe.
Increased Hydrocarbon Emissions
Catalytic converters work by reducing the levels of hydrocarbon emissions exiting a vehicles tail pipe. A bad catalytic converter can lose its emissions-lowering capabilities and cause an increase in exhaust hydrocarbon emissions, a condition that is normally picked up when a vehicle is undergoing a routine smog inspection.
Reduced Fuel Economy
Any obstruction and/or abnormality in a vehicles exhaust system has the potential to reduce vehicle gas mileage by creating exhaust back pressure within a vehicles engine. A bad catalytic converter can cause a reduction in vehicle fuel economy if it restricts the flow of engine exhaust to the point of causing a marked increase in engine exhaust back pressure.
Wednesday, April 23, 2014
Composition of Catalytic Converters
Catalytic converters chemically change toxic car emissions into relatively harmless substances like water vapor and carbon dioxide. The U.S. Environmental Protection Agency required the devices on all new cars in the United States in 1975. Since then, the converters have prevented millions of tons of harmful carbon monoxide, unburned hydrocarbons and nitrogen oxides from turning into air pollution, according to an industry group, CatalyticConverter.org.
Catalysts
A catalyst is a material that starts or speeds up a chemical reaction. Catalytic converters use combinations of precious metals as catalysts to transform toxic gases in engine exhaust. Platinum and rhodium cause nitrogen oxides to separate into harmless oxygen and nitrogen. Platinum and palladium help oxidize carbon monoxide and unburned hydrocarbons. The metals used as catalysts are valuable. About half of all converters are recycled to reclaim their catalyst metals.
Housing and Core
Converters usually have a stainless steel outer shell coated with a thin layer of aluminum. The inner core is often made of a ceramic honeycomb coated with an extremely thin layer of the catalyst material. A honeycomb structure is used to maximize the catalyst surface area that the exhaust gases contact.
Emission Control
Sensors monitor exhaust emissions before and after they go through the converter and relay the information to an emission-control system. The control system uses data on oxygen levels to adjust the vehicles fuel injection, maintaining the air-to-fuel mix needed for the converter to operate at maximum efficiency.
Tuesday, April 22, 2014
How to Adjust the Speed on a 150CC Gas Scooter

150 CC gas scooters provide a fun and convenient way to get around town. Unfortunately, as time goes on, these scooters often lose speed. Additionally, because they are technically motorcycles and not mere scooters, sometimes their speed can be too great for certain driving situations. Both scenarios require you to adjust the speed on your 150cc gas scooter. Though there are many methods for adjusting the speed of your 150cc gas scooter, the safest and easiest legal method for adjusting the speed is removing or inserting a speed inhibiting washer in the variator compartment.
Instructions
- 1
Remove the bolts holding the cover of your scooters variator in place. The variator is a part of your scooters transmission system. It looks like two large sprockets connected by a rubber belt. There will be anywhere between six to ten bolts holding the cover in place.
2Remove the lug nut holding the toothed sprocket in place.
3Remove the transmission washer from the peg that is connected the belt to the toothed sprocket to increase your scooters speed or add a washer to the peg to decrease your scooters speed.
4Replace the lug nut holding the toothed sprocket in place.
5Replace the bolts holding the cover of your scooters variator in place.
How to Remove the Ashtray of a 2007 Dodge Charger
The Dodge Charger debuted in 1966. Marketed as a muscle car, the Charger appealed to both young and old during its 12-year production run. Dodge manufactured a subcompact car bearing the Charger name from 1983 to 1987. In 2006, Chrysler brought back the full-size sedan, which adopted many styling cues from the 1960s Chargers. The third-generation Charger features a Chrysler 3.5-liter V-6 or Hemi V-8 engine and a number options and accessories. Although some accessories are nearly impossible to repair or replace, removal of the ashtray requires only a few basic tools.
Instructions
- 1
Pry up the chrome ring from around the shift lever using a tapered fiber stick or a small protected flat-blade screwdriver. Remove the ring, and set it aside.
2Remove the rubber mat from the center console, and set it aside.
3Remove the two screws that hold the shift lever bezel.
4Pry up the shift lever bezel using a fiber stick or a small protected flat-blade screwdriver. Remove the bezel, and set it aside.
5Apply the parking brake, and move the shift lever to "Drive."
6Pry off the ashtray housing using a tapered fiber stick or small protected flat-blade screwdriver. The housing is held in with clips on the side; you may have to rock the housing slightly to slide it over the clips. Remove the housing, and set it aside.
7If the Charger has heated seats, disconnect the wire harness to the switches. Tilt the ashtray, and remove it from the opening.
Monday, April 21, 2014
How to Tell a 400 Small Block From a 350 Small Block

In 1955, Chevrolet unveiled the companys first overhead valve small block V-8 engine. Initially, the small block Chevrolet engine featured 265 cubic inches of displacement. During the 1968 model year, Chevrolet began production of a larger displacement, 350 cubic inch small block engine. The higher performance small block Chevy came about in 1970, which required changes to the internal design in order to accommodate the larger cylinder bores. Identifying whether or not your particular vehicle has a 350 or 400 small block Chevy engine is an easy task, provided you have the correct information.
Instructions
- 1
Open your vehicles hood and allow the engine to cool, if applicable.
2Examine the rear of the engine block, on the drivers side, below the cylinder head to locate the manufacturers casting numbers. The casting numbers for your engine will be located below the "GM" stamp at the rear of the block. Utilize a flashlight if you have issues reading the casting numbers on the engine block.
3Write down the engine block casting numbers on a piece of paper.
4Cross-erence the engine block numbers using a suitable chart guide to find out your engines displacement.
How to Hook Foglights to a Toggle Switch

Installing a toggle switch into your fog lights electrical circuit allows you to control them remotely. Flipping the switch to the "on" position completes the electrical circuit and allows power to flow from the battery to the lights, while flipping the switch to the "off" position breaks the circuit stopping the flow of electricity. Always remember to disconnect the positive battery cable from your batterys positive terminal before servicing any electrical circuit on your vehicle. Failure to follow that simple safety step can result in painful electric shock and damage your vehicles electrical components.
Instructions
- 1
Cut the wire connecting your fog lights to their power source using your diagonal pliers.
2Remove 1/4 inch of insulation from both new ends of the power wire with your diagonal pliers.
3Connect the wire running to your power source to the "source" terminal of your toggle switch.
4Connect the wire running to your lights to the "accessory" or "load" terminal of your toggle switch.
5Cover all exposed conductors with electrical tape.
Sunday, April 20, 2014
Homemade Tow Bar

In its simplest form, a tow bar is simply a straight piece of rigid material that is attached from the towing vehicle to the vehicle being towed. The idea is that your car or trailer can be towed while not changing the distance to the car that is towing.
Simple Bar
You can make a very simple tow bar by simply cutting a 6-foot piece of 4-by-4 or even a tree trunk with a 4-inch diameter. Drill a 1-inch hole in each end, and take a 10-foot piece of 1-inch nylon cord and run it through the holes. Wrap the cord several times around the piece; tie it off and then tie it securely to the bumpers or toe hitches of each car or trailer. This apparatus should only be used if nothing else is available.
More Sophisticated Bar
Take a 1-inch piece of galvanized pipe and two u-clamps mounted on 7/8-inch bolts. Slide the 7/8-inch bolt on the clamp into the pipe and weld around the end. You can now attach the the u-bolts to the towing hitches on each car with a 3/4-inch bolt. If you want a more structurally sound bar, you can weld a triangular support system.
Some Warnings
Before towing make sure that your bar is well in place. You should use the wooden bar only in an emergency. The galvanized pipe bar is stronger; be sure you have welded it securely.
My Mercedes E320 Wont Start Troubleshoot

The E320 is a four-door sedan made by Mercedes Benz. If you cant get your E320 to start, there are several things that you can do to troubleshoot the problem. Your issue could be occurring due to low fuel level, a bad alternator, or a low charge on your battery. Your E320 might have a dead battery, which would need to be replaced. You dont have to be a certified mechanic to get your E320 up and running. You can do it yourself with little knowledge of the subject.
Instructions
- 1
Insert your key into the E320s ignition and turn it. Listen for a "clicking" noise. If you hear the clicking noise, you will need to have the car towed to a garage to have the alternator replaced.
2Look at the fuel gauge while the key is in the ignition. Add gas to the car if needed and then try to start the E320.
3Open the E320s trunk and locate the battery. Make sure that the battery terminals are connected to the battery properly. You can tell this by the "+" and "-" signs on the terminals and the connecting wires.
4Connect jumper wires to the "+" and "-" terminals on your battery and then connect the other end of the jumper wires to a different car battery. Start the other car with the wires connected and then try to start your car.
5Leave the E320 running for about 15 minutes to allow the battery to charge. Turn the E320 off and wait for a couple of minutes. Start the E320 again. If the car will not start, you need to replace the battery.
Saturday, April 19, 2014
How to Troubleshoot a Ford Taurus Alarm System
Newer Ford Taurus cars are equipped with a car alarm that protects your vehicle from getting stolen or broken into. It is a good idea to arm your car anytime it is out of your sight. However, the car alarm can cause nuisance if it goes off when its not supposed to or malfunctions. It can cause panic instead of relief. Troubleshooting and fixing the problem with the alarm may help ease any frustrations and keep you from having to get your Taurus serviced.
Instructions
- 1
Check all the car doors to ensure that they are all latched tightly. The dome light in your Taurus will usually indicate if one of the doors is open. All doors must be secured before you leave your car to keep the alarm from sounding.
2Replace the battery in your key fob. If the battery runs low, it can send unnecessary signals to your alarm system.
3Make sure there is nothing is blocking the radio waves from your remote control to your Taurus when you are using it. Remove any obstacles between you and your vehicle.
4Make sure you aim directly at the car. Some Taurus are not sensitive enough to receive signal from the car alarm remote control if you are a certain distance away.
What Can Stop a Manifold Leak
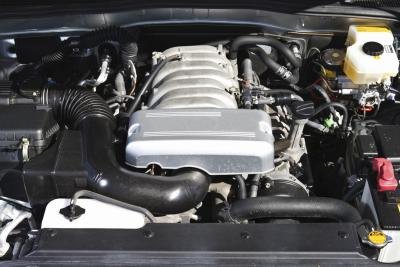
A hissing noise coming from the engine of your vehicle combined with liquid spillage from the car can mean trouble for your vehicles exhaust or intake manifold. Such signs can be symptomatic of a manifold leak, which is when your exhaust or intake manifold leaks oil or coolant. If you notice a manifold leak, its important to stop the leak immediately because it can pose a hazard to the passengers in the vehicle.
Repairing the Manifold
If the manifold is leaking due to damage to the exhaust or intake manifold, or the general wear and tear of it, then the most effective way to stop the manifold leak is to repair and replace the manifold. A manifold can be removed from the vehicle and replaced with something new so that the vehicle no longer leaks. If the manifold just has some small cracks in it that are causing the leak, another repair alternative is to have the cracks welded together rather than purchasing and installing a new manifold.
New Gasket
A new gasket that seals the manifold is one way to stop a manifold leak. If a gasket is cracked, it is no longer able to seal and maintain the connection with the manifold, thereby creating a gap between the manifold and the exhaust pipe. Shear stress to the gasket of the manifold is part of the normal wear and tear of the vehicle due to the thermal contraction and expansion that happens each time the engine is turned on and off.
Sealant Solution
You can try to stop a manifold leak by coating the gasket or manifold with a leak sealant. Leak sealants, which are available at auto repair shops, are applied directly onto the affected area of the vehicle and act as a means of sealing the leak so that no more fluid can be lost. This solution is simpler than attempting to replace the manifold or gasket.
Accurate Assessment
A manifold leak can only be stopped if youve isolated the problem accurately. If you misdiagnose the cause for the leak, or think its the exhaust manifold when its really the intake manifold, then you risk prolonging the repair and, meanwhile, the vehicle continues to lose fluids. An accurate assessment is necessary for stopping a manifold leak, so its important to learn how to diagnose and troubleshoot the problems and locate the source of the leak.
Friday, April 18, 2014
Creative Ways to Patch an Auto Exhaust Pipe

The exhaust system of a car is designed to carry away the harmful and toxic gases produced by the engine. The quicker these gases can be channeled away from the engine, the better its performance. Even the smallest crack or hole in the exhaust can reduce the overall efficiency of the car. There are numerous ways to patch an exhaust; however, some are better than others.
Cut a Section Out
If there is only one small section of the exhaust pipe that is damaged, you can simply remove it. This is a simple procedure that can be done with basic tools. All that is needed is a pipe cutter, a welder and a good eye. The biggest problem with cutting away a section of the exhaust pipe is getting to it. Unless you have a sunken pit in the garage, some jacks may be necessary to raise the car. By cutting away the damaged section, and welding the remaining pipe back together, the exhaust will still be able to function. However, efficiency will be lost. Pieces of pipe can be purchased from garages that will join together and replace a damaged section of pipe. This can prevent the exhaust pipe from becoming too small.
Heat-Resistant Material
The problem with attempting to patch an exhaust without using proper equipment is that the exhaust heats up considerably. Most material applied to patch a hole in an exhaust will burn away after the car has driven a few miles. A creative solution is to use fire-retardant and heat-resistant clothing, available from work clothing outfitters. Basic heat-resistance gloves can withstand temperatures up to 1,500 degrees Fahrenheit. This is more than capable of coping with the 300 to 520 degrees Fahrenheit that is the average temperature of an exhaust. Using a glove or piece of material to stuff into a hole is only a temporary measure, however, as the material may become dislodged as the car travels.
Use a Bandage
Not the most creative solution, but one that works, is heatproof gum. A small crack or a hole can be quickly patched up by applying this versatile material, available from most garages and hardware suppliers. The heatproof gum can come as a paste, a gum or as an actual bandage that you can wrap around any damage on the exhaust. The material is treated to ensure it can withstand the temperatures of the exhaust, and some brands of heatproof gum are designed to act as a permanent solution rather than a temporary measure.
How to Replace Windshield Washer Pump on 1998 Pontiac Grand Prix

Replacing the washer fluid pump in a 1998 Pontiac Grand Prix can help increase visibility through your windshield. The process of replacing the pump should take no more than a half-hour, and you can purchase the tools and materials your need at an auto parts store.
Instructions
- 1
Open the hood. Remove the washer fluid tank bolts with a 3/8-inch drive ratchet and socket.
2Pull the entire washer bottle assembly out from under the hood. Detach the hoses from the bottle. Do this gently, so as not to stretch or rip the lines.
3Remove the old washer fluid pump by pulling it upward toward the top of the washer fluid bottle. The pump is locked in place by the washer fluid bottle itself.
4Install the new washer fluid pump onto the bottle.
5Reinstall the washer fluid bottle hoses. Reattach the washer fluid reservoir to the vehicle.
Thursday, April 17, 2014
Advantages of Stainless Steel Exhaust

An exhaust is an important vehicle component that funnels and scrubs engine byproducts while reducing engine noise. Stainless steel is one of two basic types of exhaust materials. The other material is regular steel. Stainless steel exhausts are less likely to rust and can be visually more appealing.
More Durable
A stainless-steel exhaust is less prone to rust, according to the online automotive magazine Matey-Matey. The rust process is extremely slow, compared with regular steel that can rust within three years of use. Stainless steel exhausts vary by grade: The lower the grade; the better the exhaust. For example, 304 and 316 grade exhausts are superior to a 409-grade exhaust, which offers less resistance to corrosion, though still better than regular steel.
Visually Appealing
Stainless steel is more visually appealing, because its not likely to rust and discolor. In addition, these exhausts initially have a polished finish and brilliant shine. As long as you keep the exhaust system clean, the finish retains its original appearance and does not tarnish.
Emits Fumes Faster
According to Stainless Online, a stainless-exhaust kit manufacturer, stainless-steel exhausts are more efficient ventilation systems, which reduces heat buildup in the engine. This may justify their increased cost. Matey-Matey says several stainless steel exhausts come with a lifetime guarantee.
Life-Time Guarantee
How to Use a Cotter Key
Cotter keys (also known as cotter pins) are small metal fastening devices. The come in a variety of sizes but are all used for the same purpose, safety. Cotter pins are used to insure that a bolt or a pin does not come unscrewed or slide out of its hole. This very simple device can prevent serious damage to equipment and those working with it.
Instructions
Inserting the pin
- 1
Locate the hole in the bolt.
2Push the cotter pin through the hole. Ensure that the pin goes all the way through.
3Bend each side of the pin to wrap it around the bolt with your needle-nose pliers. This will ensure that the cotter pin will not slide out.
Removing the cotter pin
- 4
Use a needle-nose pliers to straighten the sides of the cotter pin.
5Insert one of the ends of the needle-nose pliers into the circular end of the cotter pin.
6Pull the pin straight out with one motion.
Wednesday, April 16, 2014
How to Replace a Valve Lifter

Valve lifters are the actuators that open and close the valves on top of the engine, allowing the appropriate quantity of air into the cylinder. As with most moving parts under strain inside an engine; dirt, heat and friction take their toll over time, and the lifter will become worn, degrading its performance, and increasing the possibility of damaging other components.
Instructions
- 1
Remove the intake manifold and valve covers. Set them aside and take note of how all the bolts were positioned. Looking down into the engine, you should now be able to see the heads of the valves. But the push-rod will be passing over the top, preventing you from removing them.
2Remove the rocker arms and push-rods. With all the upper hardware on the engine disassembled, the cylinder head can be unbolted and lifted off the rest of the engine, giving you access to the tappets below. With the tappets released and removed, the lifters are accessible and ready to be removed.
3Grip the heads of the lifters with the needle-nose pliers and caully lift them up and out of their respective recesses. Lower the new lifters into the hole and replace the tappets. The tightness of the tappets is a trial and error process for mechanics who lack professional measuring equipment, so you may need to adjust them after the engine has been rebuilt. If the engine runs roughly, they need to be loosened. If they make a tapping noise, they need to be tightened.
4Replace the push-rods, rocker arms, valve covers and intake manifold, ensuring all bolts are properly tightened. Start the engine and allow it to run for five minutes, then stop it and make the necessary tappet adjustments. Repeat until the engine is running smoothly, allowing it to cool for several minutes between each run.
What Instrument Is Used to Test the Condition of a Spark Plug
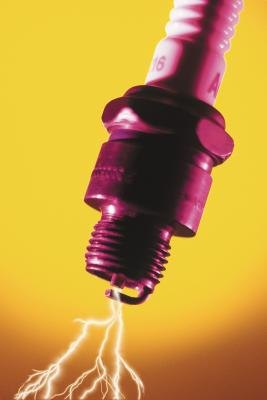
While the computerized engine management systems that run todays cars are extremely complex and require increasing specialized diagnostic equipment and tools, all gasoline-burning engines must still have spark plugs. The plugs allow a properly timed spark of electricity to jump through the flammable mixture introduced into the top of the piston chamber, causing ignition. Ascertaining their condition is done more through familiarity and interpretive knowledge than through the use of a single piece of equipment.
Know Your Plugs
The terms cold plug and hot plug are often used, and a knowledge of what to expect from the plug is necessary in determining its condition. The terms er to the ability of the material that the plug is made from to transfer heat, in this instance from the point at which the spark occurs into the engine block for dissipation. A cold plug transfers heat quickly and does not work well at extremely high temperatures. A hot plug transfers heat poorly, allowing heat to build up to approximately 1,550 degrees Fahrenheit, and is designed to work in that way; hot plugs are less susceptible to fouling because they burn off contamination. Identification is a question of experience: In general, hot plugs have longer insulator tips.
Visual Condition
Always allow an engine to fully cool before attempting any service work, including the removal of spark plugs. If the insulator tip of a plug that has been in service looks pale gray, or pale gray with a yellow or brown tint, the engine is running correctly, the spark plug gap is set correctly and the plug is torqued correctly into the receiver. Dull, black carbonization on the tip suggests that too-cold plugs are in use, and they should be replaced with hotter-running units. As with all visual indications, this symptom could also indicate problems elsewhere in the engine, in this instance a bad fuel mixture. Melting at the electrode indicates either that the plug was incorrectly torqued into position or that the heat range of the plug is not as suggested for the engine.
Gapping
The space between the electrode and the insulator tip must be exact for the plug to function correctly. Spark plug gap-testing tools are a set of wafer-thin blades -- each blade looks something like a fingernail cleaner -- that rotate on a pivot in and out of a case. These tools used to be ubiquitous in every do-it-yourselfers and professionals kit, but modern engines and plug technology have made them all but redundant. New plugs are now delivered with the gap precisely set and do not deform under any but the most extreme of engine conditions. If a modern spark plug gap changes under use, that is a symptom, not a cause; the cause must be determined by engine diagnostics and the plug set replaced after rectification of the fault.
Equipment
An array of equipment is available to test spark plug condition, but the visual checks suggested and a regular maintenance schedule make the investment practically unnecessary, even for the professional. The spark plug gapping tool is, as noted, all but redundant in modern vehicle maintenance practices. Working according to the manufacturers instructions, it is possible to use a volt-ohmmeter to ascertain the circuit load.
Voltage Testing
Metered spark gap testers are available that plug into the coil to measure the jump of the spark. Capable of handling current between 0 and 40,000 volts, the tool diagnoses faults in the coil, the ignition wires and the plugs.
Testing Spark Plug Wires
Inline spark testers that use a bulb do not give a metered reading, but they do give an instant indication of whether a coil-wire-plug circuit is operational. The device is inserted between the plug and the wire, after you have first removed the wire from the top of the plug. When the engine is turned over a bulb flashes if the circuit is functional but does not flash if it is faulty. Compact ignition testers are extremely simple to use to verify that there is a spark to the plug. Fitted into a plug wire end and clamped to the engine, they should spark when the engine is turned over. If they do not, there is a problem upstream of the device.
Tuesday, April 15, 2014
The Location of the Cam Position Sensor on the 1992 Park Avenue
Before changing the camshaft sensor on your 1992 Buick Park Avenue, you must determine its location on the engine; the sensor is tucked away under the water pump, and while you can see it from the top of the engine, replacing it requires you to work under the front of the car. A replacement sensor is available from most auto parts stores or through a Buick dealership.
Instructions
- 1
Open the hood of your Park Avenue and locate the water pump on the front of the engine. You will see the water pump is the front-center of the engine block.
2Look near the base of the water pump pulley, along the bottom edge: You will see an electrical connector and harness.
3Follow the harness in toward the block, until you can see a small, round sensor threaded into the block--this is the camshaft sensor.
How to Clear Codes on the 1985 Toyota Truck

On-board diagnostics (OBD) computers were put into vehicles in the early 1980s to monitor and troubleshoot problems within vehicles. To clear the codes in your 1985 Toyota truck you need only an end wrench and a few moments of your time. Clearing the codes will turn off all lights such as "Check Engine" or "Service Engine Soon" from your instrument cluster. Make sure you have all repairs and servicing done before you clear the codes to allow the OBD computer to function properly.
Instructions
- 1
Check to make sure your ignition is completely off. Then pull the hood release lever.
2Locate the battery under the hood. Find the negative terminal on the battery. Look for a retaining nut attached to the clamp and loosen it using the end wrench.
3Slip the clamp off of the negative terminal, taking care to keep it away from the positive side of the battery.
4Wait a minute and then put it back on the negative terminal. Tighten the nut with the end wrench. Lower the hood.
5Put the key into the ignition and start the truck. Look on the instrument panel to make sure all the lights are off.
Monday, April 14, 2014
How to Blacken Bumpers

Black bumpers can appear faded after a few years of constant exposure to the elements. Wax and polish can also build up on your bumper, causing it to appear dull and worn out. There are a few simple methods to achieve that fresh from the factory look.
Instructions
Prepare the Bumper
- 1
Remove the bumper from the car. Your bumper is bolted on and can be removed with a basic Phillips-head screwdriver. While this may seem tedious, it will save you time in the long run and give you more room to work. You will also be able to inish the entire surface area.
2Buff your bumper with fine sandpaper. This will remove any excess wax or polish. Rubbing alcohol will also release stubborn wax.
3Wash the bumper with soap and water. This will eliminate all the grit from the sandpaper as well as clean off excess dirt and debris. You should already see a difference in the condition of your bumper.
Blacken the Bumper
- 4
Use a heat gun. Start by heating the bumper from a good distance away and gradually coming closer until you start to see a difference. The plastic will melt and you will have a smooth finish. Heat guns are available for around $20 at a home improvement store like Lowes, Home Depot or Ace Hardware.
5Use a back-to-black kit as an alternative to using a heat gun. You can find these for under $10 at auto part stores. These can fade over time and are only a temporary solution.
6Use a coat of black spray paint with a satin finish if you are only painting black plastic strips on your bumper. Do not use this on a fully black non-plastic bumper.
Nissan Titan Headlight Aftermarket Running Light Installation

In 2004, Nissan introduced the Titan, a full-sized pickup truck available in the North American market. This truck comes standard with daytime running lights that are set low in the front bumper. If you want to install aftermarket lights either because the originals were damaged or you simply want to personalize your Titan, do not take it to a garage. This repair is easy to do at home making it the perfect do-it-yourself project for a Saturday afternoon.
Instructions
- 1
Park your Nissan Titan on a flat level driveway or parking lot. Apply the parking brake and turn the engine off. Depending on how long the truck has been running, you may need to wait up to 30 minutes for the truck to cool.
2Slide under the front end and look directly behind the running light lens. Here you will find an access panel covering the inner workings of the running light assembly. Pry it off with a flathead screwdriver.
3Locate the wiring harness which connects the Titans electrical system to the running lights socket. Grab the harness by the plug end. Squeeze the two side tabs and pull to release the harness.
4Unscrew the three retaining bolts holding the light assembly to the Titans bumper. Use an adjustable wrench for this step. Place the bolts aside, but do not lose them as youll need them to secure the aftermarket running light.
5Slide the old light assembly out and then insert the aftermarket assembly. Secure it with the three retaining bolts. Plug the wire harness into the socket. Snap the access panel back in place. Then repeat this entire process for the remaining running light.
Sunday, April 13, 2014
What Does a Map Sensor Control

MAP is an acronym for manifold absolute pressure. A MAP sensor is an electronic control that works in conjunction with the intake manifold, a system of tubes and chambers that carry a mixture of air and fuel to the intake valves.
Function
A MAP sensor measures the pressure of the air channeled to the carburetor before it passes through the intake manifold. The signal that the MAP sensor emits changes in accordance to the pressure it detects.
Signals and Changes
The MAP sensors signals helps the engine control module determine what changes need to be made in the fuel mixture. these changes include how much fuel is injected and when cylinders are ignited.
Importance of Readings
Without accurate readings from the MAP sensor the proper air-fuel mixture is not maintained. This has a direct effect on the performance of the engine.
Faulty MAP Sensors
If the MAP sensor malfunctions, the "Check Engine" light should come on, although it may not stay lit. Engine performance will be drastically reduced. One common performance issue is hesitation when attempting to accelerate. This is a result of the loss of horsepower that is characteristic of a vehicle has a bad MAP sensor.
Bad MAP sensors also contribute to an increase of auto emissions.
How to Change a Head Light on a 2007 Mazda 3
The headlight replacement process for a 2007 Mazda 3 depends entirely on whether or not the specific vehicle has a turbocharger. Although both types use the same HB3 bulbs for the the high beams and H7 bulbs for the low beams, accessing the lights is what differs. As the headlights on any vehicle are important for the safety of the driver and passengers, they should be replaced as soon as they burn out.
Instructions
Accessing the Headlights (without Turbocharger)
- 1
Turn the ignition switch off and open the hood.
2Rotate the screws counterclockwise and remove them from the headlamp assembly, using the screwdriver. Remove the cover.
3Disconnect the electrical cord from the rear of the assembly.
Accessing the Headlights (with Turbocharger)
- 4
Turn the ignition switch off and open the hood.
5Remove the plastic clip above the headlamp assembly and pull the slide mount up to a position where it does not interfere with the frame. If replacing the left-side headlight, remove the strap and take out the air filter.
6Disconnect the electrical cord from the rear of the assembly.
Replacing the High-Beam Bulb
- 7
Rotate the socket and bulb assembly counterclockwise to remove it.
8Remove the headlight bulb from the socket by pulling it straight out.
9Disconnect the bulb from the electrical connector by pressing down on the tab with your finger and pulling the bulb upward.
10Connect the electrical connector to the new bulb and place it back into the socket and the assembly.
11Rotate the socket and bulb assembly clockwise to lock it.
Replacing the Low-Beam Bulb
- 12
Pull the sealing cover off of the headlamp bulb.
13Unhook the bulb retaining spring and swing it outwards to free the headlight bulb.
14Pull the bulb straight out and replace it with a new bulb.
15Swing the spring back into place and reattach the sealing cover.
Saturday, April 12, 2014
R134a Retrofit Procedures
All pre-1994 vehicles that are equipped with air-conditioning were initially filled with R12 rigerant. This rigerant was eliminated in favor of the "ozone-safe" R134a rigerant. If your R12 filled vehicles air-conditioning is operating properly and not leaking, there is no reason to retrofit it for R134a rigerant. However, if the air-conditioning requires repair, a retrofit is necessary as R12 is not only harmful to the environment, but scarce in quantity.
Lubrication
The oil used to lubricate the compressor can become contaminated from the R12 freon. This is not a concern when R12 is continuously used. However, when retrofitting, the key component is to remove all remnants of the R12 freon. For this reason, you must flush and drain the compressor oil and replace it with new PAG oil.
Seals
The rubber O-ring seals have small pores, and the R12 freon particles can become trapped in those pores. For this reason, all auto manufacturers recommend that the O-rings throughout the air-conditioning system be removed and replaced with R134a-compatible seals. There should be anywhere from 5 to 10 O-rings in any air-conditioning system.
Small Components
Most air-conditioning systems have several small components throughout that you should replace to properly retrofit an air-conditioning system. There are two filters that you should replace -- the receiver/drier and the orifice tube. You should also replace the expansion valve, if easily accessed, as well as the high-pressure cut-off switch. All of these components will have remnants of R12 freon and can cause cross-contamination with the R134a.
Check/Fill Ports
The check/fill ports, also know as the high and low service ports, are the components used to check system pressure and fill the system with rigerant. This ports are completely different from R12 ports; theore replacement is required to recharge the system, let alone the small remnants of R12 freon present.
Evacuation, Flush and Recharge
The air conditioning system, while low on freon, may still have a small amount remaining throughout. For this reason, a proper evacuation -- removal of freon via suction -- is required, and must be performed by a technician certified for R12 handling. A good addition to the evacuation is a complete system flush, but it is not required. After the system is free of R12 freon, you must fill it with R134a. Only fill the system to 85 to 90 percent of its capacity listed on the under-hood placard. Keep in mind that a certified reclamation company must properly dispose of the evacuated R12 freon.
Labeling
While the R134a fittings on the service ports should be enough to deter a technician from mistakenly putting R12 freon in the system, some inexperienced mechanics may use an adapter and fill it with R12. Doing this will completely negate all of the work performed, as well as potentially cause damage to the system. For this reason, all retrofit kits are required, by law, to include several warning labels advising the mechanic not to use R12. Place these labels in several conspicuous locations, such as near the under-hood placard.
How do I Remove the Differential Cover on a Ford Ranger
Removing the differential cover from the axle on your Ford Ranger is the only way for you to access the gears inside the differential. If you need to change the gear oil, inspect the ring and pinion gears or replace seals and bearings in the differential, you must remove the cover. It will only take a few minutes and just a few hand tools to complete the job. In most cases, removing the cover is the simplest part of any job involving the differential.
Instructions
- 1
Raise the rear of your Ranger off the ground with a jack. Position a set of jack stands under the rear axle tube to support the truck. Lower and remove the jack.
2Position a large oil drain pan under the rear differential. Locate the bolts around the outer edge of the cover. Loosen all the bolts with a socket and ratchet. Remove them one at a time, starting at the bottom.
3Leave the top bolt in place and use a wide putty knife to pry the bottom of the cover away from the differential housing. Oil will begin to drain from the differential, so make sure the pan is under it and catching the oil as it comes out.
4Remove the last bolt at the top of the cover and lift the cover off the differential. You can now perform whatever work is necessary before reinstalling the cover with a new gasket.
Friday, April 11, 2014
How to Check for an Air Leak in My Vans Air Conditioner
A sure sign of air conditioning problems is a lack of cool air coming out of the vents in your van or other vehicle. The problem might be with the compressor or motor, but it might just be a leak. The leak might not be your only issue, but it must be addressed before fixing any other components of the air conditioning system.
Instructions
- 1
Look in your vehicles owners manual to determine what type of rigerant your van uses.
2Set the rigerant leak-detector to the appropriate setting. The setting varies based on the type of rigerant your vehicle uses. It is typically labeled CFC, HCFC or HFC, and must be set correctly to locate the source of the leaks.
3Move the rigerant leak-detectors sensor along the air conditioning hoses and other components, looking for the indicators of a leak. The indicators vary in different rigerant leak-detectors, but are often represented by a buzzer or other sound.
4Pay special attention to connection points. Move the sensor across all sides of the hoses and other components.
5Mark each leak with masking tape. This allows the mechanic addressing the leaks to easily locate it.
How to Find Part Numbers for My Chevy Silverado

Chevrolet designs, manufactures, and markets the Silverado, a full-sized pick-up truck. The term "Silverado" was first used to describe a trim package on Chevrolet pick-up trucks beginning in 1975. For repair and maintenance of Silverado pick-up trucks, owners need to be able to find the correct parts.
Instructions
- 1
Go to the Auto Parts Giant website. (See Resources.) Select the "Year," "Make," "Model," "Sub model (if applicable)" and "Engine Size" for your Silverado. Press "Go." Type the part that you are looking for into the "Search" box. Press "Search." Review the results and identify the part you are looking for. The part number appears in the product description.
2Go to the Napa website. Click "Select a Vehicle" and click the features that match your Silverado truck, such as "Year." Enter the part you are looking for in the "Part Number Search" box. Press "Search." The results display the part number.
3Launch the Auto Zone web page. Click "Manage My Vehicle" and "Add A Vehicle." Select the details for your Silverado truck and "Look Up Parts." Click on the appropriate category and the specific part to view the part number.
Thursday, April 10, 2014
How to Replace a License Plate Light on a 2002 GMC Envoy
The license plate light bulb on a 2002 GMC Envoy is directly above the rear license plate inside a small, plastic housing and comes on when the headlights are on. At night, the light bulb illuminates the license plate information. In many states, it is illegal to drive a vehicle with a burned-out license plate light bulb. A replacement light bulb can be found in any store that sells automotive parts. Replacing the light bulb is very easy and should be done as soon as you discover the light bulb is burned out.
Instructions
- 1
Shut off the engine and make sure the vehicle is in park. Apply the parking brake.
2Use a Phillips head screwdriver to remove the two screws securing the license plate light assembly to the tailgate. Put the screws in a secure place.
3Gently pull the light assembly out of the tailgate to expose the light bulb. Pull the faulty light bulb out of the socket and discard it.
4Push the new light bulb into the socket and make sure it is tight. Reposition the light assembly on the tailgate and secure it with the two screws. Tighten the screws; do not overtighten.
5Turn on the headlights to make sure the license plate light bulb illuminates.
Buicks Recommended Maintenance Schedule for a 99 Buick Regal
The Regal started out as a top trim level on the Buick Century in 1973, and five years later split off to become its own model. That was good timing, too; while earlier Centuries had been beautiful and stylish cruisers, by 1978 the car was set to devolve into a terrible little hatchback. The Regal, though, went on to both parent the awesome Grand National and GNX, and to carry the Buick performance banner through the companys retirement-home years.
Time Schedules
Most maintenance schedule intervals measure in miles of use, but some go completely by time. Oil change intervals, oddly, are one of them. General Motors recommends changing the oil only when the oil life monitoring system tells you to, or every 12 months -- whichever comes first. Every six months, you should inspect the brake system pads and lines, the CV joint boots for grease leakage, the cooling system hoses and clamps, the exhaust, fuel, steering, suspension and throttle systems. Realistically, unless you never drive the car, these six-month inspections should line up pretty closely with the O-dictated oil change intervals.
Service Schedules
Manufacturers give two different types of service schedules. The "Normal" service schedule should apply to most drivers, but thats rarely the case in the real world. "Severe" service schedules are more intensive, designed to help keep cars running when they encounted car-killing conditions like lots of stop-and-go driving, extremely high or low average temperatures, bad road conditions and dusty or dirty air. In this case, the primary difference is that the Normal service schedule comes in 7,500-mile increments, and the Severe schedule comes in 6,000-mile increments. Apart from that, the Severe schedule requires air filter inspections every 15,000 miles, and filter replacement every 30,000 miles.
Normal Service Schedule
Starting from the very first interval, which your car has long since passed: Rotate the tires every 7,500 miles and replace the cabin air filter every 15,000 miles. At 30,000 miles, perform the above and replace the engine air cleaner element, inspect the supercharger lubricant if so equipped and inspect the fuel tank cap and lines regardless of when you did it on the time interval. At 60,000 miles, do all of the above and inspect the engines serpentine drive belt. Do all the same things at 90,000 as you did at 60,000. At 100,000 miles, replace the transmission fluid and filter, inspect the spark plug wires for cracking and damage, and replace the spark plugs. Perform the same service at 120,000 as you did at 60,000. Start the whole cycle over at 127,500 miles.
Severe Schedule
Rotate the tires every 6,000 miles; at 15,000 miles, replace the cabin air filter and inspect the engine air filter for dirt and clogging. If you can see light through it, it should be fine. At 30,000 miles, do all of the above but replace the engine air filter, inspect the supercharger lubricant if so-equipped and inspect the fuel system. Do the same at 45,000 as you did at 15,000. At 50,000 miles, replace the transmission fluid and filter. At 60,000, rotate the tires, replace the cabin filter, replace the engine air filter, inspect the supercharger lubricant, and inspect the fuel system and the drive belt. Do the same at 75,000 as you did at 45,000, and do the same at 90,000 as at 30,000. At 100,000, replace the spark plugs, inspect the plug wires and replace the transmission fluid and filter. Do the same at 120,000 as at 60,000, and start the cycle over at 126,000 miles.
Special Notes
If youve just bought the car or youve lost track of the servicings, then perform every maintenance task to "reset" your service schedule clock. Replace the oil even if the O doesnt specify it, and start over from Mile Zero by replacing the air filter element, cabin filter, serpentine belt and spark plugs. Inspect the fuel system and oiling system, rotate or replace the tires, inspect the plug wires, and grease all of the grease fittings on the chassis. However, if you dont know the cars history, then DO NOT, under any circumstances, get a full transmission flush. Old fluid breaks down and develops a unique chemistry of its own, and completely new fluid circulating between the transmissions clutches may not mix with old fluid soaked into the clutch material. The result: slipping and burned clutches, and a fried transmission. If youre starting over from Mile Zero with a full maintenance regimen, just perform a filter change and transmission fluid drain-and-fill, then another drain-and-fill at 6,000 and 12,000 miles. This gradual method of replacing the transmission fluid will give your clutches time to absorb and acclimate to the new fluid without slipping and frying.
Wednesday, April 9, 2014
How to Install the Fuel Pump on a 1997 Dodge Ram
The Dodge RAM is a series of pickup trucks in a variety of carrying capacities and trim levels. The 1997 models use multi-port fuel injection to deliver fuel to the engine under high pressure. The fuel pump in these vehicles is part of a module that also includes the fuel gauge sending unit and float. The fuel pump module in a 1997 Dodge RAM is attached to the top of the fuel tank, so you must disconnect the fuel tank to install a new fuel pump.
Instructions
- 1
Disconnect the negative battery cable with a socket wrench to ensure you dont inadvertently attempt to start the engine. Open the filler cap for the fuel tank to relieve the pressure in the fuel tank and remove the cap from the fuel pressure port on the fuel rail.
2Attach a fuel pressure gauge to the fuel pressure port and place the open end of the pressure gauges hose into a gasoline container. Open the pressure gauge to relieve the fuel pressure in the fuel system. Remove the pressure gauge from the fuel pressure port and replace the cap.
3Pump the fuel from the fuel tank into a gasoline container with a hose. Raise the vehicle with a floor jack and support it with jack stands. Disconnect the fuel line and electrical connection from the fuel gauge unit. Remove the mounting screws for the filler tube assembly with a socket wrench and disconnect the filler tube from the fuel tank.
4Support the fuel tank with a transmission jack and remove the nuts for the fuel tanks mounting straps. Lower the tank slightly with the transmission jack so you can detach the fill hose and vent hose to the fuel tank. Remove the electrical connections for the fuel tank. Disconnect the evaporative emissions line and the fuel supply line. Remove the fuel tank from the vehicle.
5Disconnect the fuel line to the fuel pump module. Clean the fuel tank around the fuel pump module with the shop towel to ensure that debris doesnt fall into the fuel tank when you replace the fuel pump.
6Turn the locking ring for the fuel pump module counterclockwise with a socket wrench. Remove the locking ring from the fuel pump module, and clean the fuel filter at the bottom of the fuel pump module. Discard the gasket for the fuel pump module.
7Install the new fuel pump module and its gasket by performing steps three through six in reverse. Tighten the locking ring for the fuel pump module to 40 ft-lbs. with a torque wrench. Fill the fuel tank with fuel and connect the negative terminal for the battery with a socket wrench.
How to Replace Struts on a 2003 BMW 330
The 2003 BMW 330 is a rear wheel drive sedan that uses independent suspension setups on all four wheels. The independent suspension relies on struts to absorb bumps in the road. However, these struts wear out like any other automotive components, and the stock OEM struts need to be replaced every 60,000 miles. Replacing the struts yourself can save you a lot of money and should only take a day for most people to do.
Instructions
- 1
Park the 2003 BMW 330 somewhere flat with a lot of room to the sides. Also make sure that you are not blocking anyone in as the car will be stuck in place until the struts are all changed out. Put it in "Park" and then turn the sedan off. Jack up the car by sliding a car jack under the jack points at each corner. When a corner is elevated, slide in a jack stand to keep the car up. Once the car is fully elevated, remove the wheels from the 330 with your tire iron.
2Unbolt the sway bar linkages from both the front and the rear wheels. The sway bars help keep the car from wallowing in the corners by connecting opposite side control arms. The bars are held to the bottom of the car by bushing mounts, but all you need to do is unbolt the ends of the bars from the bottom control arms. Rotate the ends of the sway bars down so that they are out of the way.
3Unbolt the single bottom retaining bolt on the front right strut. Use a breaker bar to wedge the bolt out as it will be firmly stuck in. Then unbolt the top three bolts at the top of the strut and use the breaker bar to wedge the entire strut out. Be caul to support the strut so that it does not fall. Then bolt in the top of the new strut into the 330s frame. Once it is supported, raise the steering knuckle up and bolt in the bottom of the strut. Repeat this process on the left front wheel as well.
4Fold down the rear seat of the 300 and pull off the plastic tab over the top of the struts. Unbolt the bolt underneath for the right rear, and then go to the right rear wheel well and unbolt the bottom of the bolt from the hub assembly. Pry the strut out with the breaker bar and place it to the side. Bolt in the new strut and then repeat the process on the left side. Replace the plastic tabs and then fold the back seat back up.
5Bolt the sway bars back into place and then put the wheels back on the 330. Lower the 330 off the stands and then look at the corners to make sure the struts are supporting the cars weight.
Tuesday, April 8, 2014
Can Black Oil Damage Your Car

Motor oil insures your cars engine runs properly and provides you with reliable transportation. The oil should be changed according to the manufacturers instructions for optimal performance and longevity.
Function
Fresh motor oil is an amber color. Black oil is oil that has collected dirt and impurities from your engine. The purpose of motor oil is to lubricate the moving parts of the cars engine so it can perform as specified. When oil is black, it means its viscosity (the ability to flow as a liquid) is impaired. It will not flow and lubricate as easily and the engines moving parts will suffer more wear from daily activities and wear out more quickly.
Solution
All car manufacturers have different standards for motor oil. The optimal amount of time to change oil is usually measured in miles. The common rule of thumb used to be 3,000 miles, but many auto manufacturers have increased that to 7,500 miles. For best results, er to your cars operation manual or contact your auto manufacturer or a qualified and licensed mechanic. It is best to er to these sources as it differs for each car.
Considerations
Black oil indicates engine health. Black oil generally means the engine requires an oil change. Engines also can use up oil as they age or are used more frequently. If the car is driven more than usual, changing the oil before the mileage limit specified by the car manufacturer is recommended.
What Is the Purpose of a Solenoid

Solenoids are used in a variety of systems, but most commonly in cars. Starters in particular use solenoids. Often when a vehicles starter is malfunctioning the solenoid is the problem.
Definition of a Solenoid
Solenoids are a type of electric motor. They are commonly used in cars as heavy duty relays. The technical definition of a solenoid is a device or motor that can produce back and forth, or linear, motion when a force is applied. Solenoids will respond to hydraulic, pneumatic or electrical force.
Solenoids as Actuators in Cars
Solenoids are mainly used in cars as actuators. A solenoid will move a component a certain distance after electricity has been applied. Starters are probably the most common actuator component. Another common usage in vehicles is as a relay. A solenoid closes a circuit when electricity is applied.
.
Types of Solenoids
Solenoids can also be used in propane, nitrous-injections and propane systems. Fuel injectors are also solenoid valves. There are different types of solenoids. The push type uses a spring to hold the solenoid closed; it opens when voltage is applied. The pull type pushes out a solenoid arm when electricity is applied. A third type is push/pull, which works in both directions.
Solenoid Mechanics
A solenoid has a coil set that it uses to induce a magnetic field on a permanent magnet. The magnet will either be attracted or repelled when power is applied to the coil. In a car, the solenoid in the starter is a relay which moves metal contacts into place which closes a circuit. The solenoid is sent an electrical current when the ignition key is turned. This triggers the magnetic field of the solenoid that pulls on the contacts, closing the circuit.
Monday, April 7, 2014
Size of the Fuel Tank for 1989 Ford Econoline

The Ford Econoline (E-150) model of van was introduced in the 1960s and had a major redesign in 1975 that lasted through 1991. As of 2010, models of this van are still in production. This van is still the base model that most commercial delivery vans are built off of, and it shares many chassis and undercarriage elements with the F-series truck.
Gas Tank Capacity
The original equipment fuel tank for the Ford E-150 van is a 22-gallon fuel tank. Replacement parts are available.
Gas Tank Placement
The E-150 places the fuel tank behind the rear axle of the van in the 1989 model; after 1992, the placement of the fuel tank was changed to accommodate a 37-gallon fuel tank.
Gas Tank Construction
Like nearly every gas tank made since the 1960s, the gas tanks for the E-150 are made out of steel, coated with zinc as an anti-corrosion barrier.
How to Recycle an Aluminum Radiator

Aluminum car radiators can be melted down to be re-formed into a variety of new aluminum products. Aluminum, including aluminum in the form of a radiator, is classified as scrap metal, and you may be able to sell it to a scrap metal recycling center in your area. The value of an aluminum radiator as scrap depends on the purity of the metal, which can be determined by examining its strength, texture and hardness, and the current market price of aluminum.
Instructions
- 1
Locate a scrap metal recycling company in your community.
2Call the local scrap metal company to confirm that it purchases and recycle aluminum radiators. Discuss the terms of the exchange.
3Arrange for pickup service, if available, or transport the aluminum radiator to the dealer. The selling price of the radiator as scrap metal will be determined by using the current market price, the weight of the radiator and the purity of the aluminum.
4Complete the sale according to the agreed-upon terms.
Sunday, April 6, 2014
How to Install a Fuel Pump on a 1979 Cadillac Eldorado
The 1979 Cadillac Eldorado had an eight-cylinder 5.7-lilter engine with fuel injection that required a low-pressure fuel system. The fuel pump in the 1979 Cadillac Eldorado pressurizes fuel to between 9 and 13 pounds per square inch. The fuel pump in this vehicle attaches to the fuel tank, requiring the removal of the fuel tank to install the fuel pump.
Instructions
- 1
Disconnect the cable on the negative terminal for the battery with a socket wrench to prevent the unintentional discharge of electricity. Open the door to the fuel tank filler, and disconnect the electrical connector for the fuel sending unit.
2Remove the protective cap for the pressure fitting on the fuel line, and connect G.M. tool no. J-5420 to the pressure fitting. Wrap a shop rag around the pressure fitting, and slowly open the valve on the tool to relieve the pressure in the fuel system. Disconnect the tool from the pressure fitting, and replace the protective cap.
3Siphon the fuel from the fuel tank into a gasoline container. Raise and support the rear of the vehicle with jack stands, and disconnect the ground wire for the fuel sending unit with a screwdriver. Detach the fuel lines from the fuel tank, and support the fuel tank with a wooden block on top of a jack. Remove the screws for the support straps of the fuel tank. Lower the fuel tank slightly, so you can disconnect the electrical connector for the fuel pump. Lower the fuel tank completely, and remove it from the vehicle.
4Remove the nuts that fasten the fuel gauge unit to the fuel tank with a socket wrench. Turn the locking ring for the fuel pump counterclockwise with a brass punch and hammer. Remove the locking ring, and lift the fuel pump from the fuel tank.
5Install the new fuel pump by performing steps 1 through 4 in reverse order. Tighten the screws for the fuel tank retaining strap to 25 ft. lbs. with a torque wrench. Start the engine, and check for fuel leaks.
What Is a Rear Ball Joint
A ball joint links the console arms of the front and rear suspensions to the wheel hub assemblies of your vehicle. In some vehicles, the ball joints connect all components of the suspension.
Significance
Rear ball joints are sometimes used in vehicles that are front-wheel drive and have independent suspensions. In some newer vehicles, the rear suspension is assembled with ball joints to link all parts of the suspension together.
Function
The ball-and-socket design of the ball joint provides swivel room for the knuckles of the joint as the wheels of the vehicle are steered. It also allows the suspension to handle changes in the road as the vehicle is moving.
Considerations
If there is a problem with the ball joint, you might hear a knocking noise when your vehicle goes over small bumps in the road. Erratic steering and wandering are also indicators of problems with the ball joint.
Saturday, April 5, 2014
How to Repair a Motorcycle Exhaust

If you have a motorcycle with a dented exhaust pipe, you can easily repair it yourself without spending a great deal of money. With just a few tools and some time, youre motorcycle exhaust will be fixed in no time. In most cases, you will be able to restore the exhaust shape by as much as 95 percent, which isnt perfect, but is quite an improvement.
Instructions
- 1
Run water through the entire exhaust system two or three times in order to ensure that its clear of fresh gas deposits (if the exhaust has excessive carbon deposits, remove all previous deposits before pressurization). Seal both ends of the exhaust and tighten the expansion block plugs (the expansion block plugs should be located far enough in to attach vice grips on each end of the exhaust). Attach the vice grips (one small one on each end).
2Hook the exhaust pipe up to an air compressor before pressurizing the system. Pressurize the system (between 80 and 120 PSI). Heat each dented area with the map gas system to a red glow slowly (the dents may start to come out), keeping the heated area pointed away from you. Tap out the dents (moving in circles around dented area) with your hammer.
3If the seams split due to excessive heat, use the welder to seam the splits back together. If you are not well-versed in the use of a welder, you may have to take the exhaust to someone who can do this portion for you. Turn on the drill with the wire wheel attachment. Apply the wheel with a great deal of pressure to any areas that are discolored until the discoloration is reduced or completely removed. Polish the exhaust using a clean towel to remove any final discoloration.
Motorcycle Wheel Chock Ideas

A motorcycle chock, or stand, is critical for storing, transporting, making repairs, and performing maintenance on your motorbike. There are many different styles available and all have their pros and cons. Some are easier to use, more durable, and more versatile than others. There are several options when it comes to finding a wheel chock for your motorcycle.
Front Wheel Chock
There are many styles of front wheel chocks available. Having to maneuver the bikes front tire into the secure holding device is something they all have in common. Their differences are in construction. You can secure some to any surface, such as a trailer or garage floor for security. Others are portable. It is possible to adjust some manually for wheel width, and for others the chock adjusts automatically. With some, you just push the bike into the frame, and it sits flat in the frame. But with others, the front wheel sits in a cradle device, which means you must push a little harder to get the tire in. See the resources for some examples and reviews of front wheel chocks.
Rear Wheel Chock
Rear wheel chocks are a design made to push the rear of the bike up and hold it under the swingarm. The ideal rear wheel chock stand should work easily in one motion. When you push the stand, it should easily lift the bike onto the stand. Rear wheel chocks help to secure the bike for routine repairs, maintenance, cleaning or storage. There are many brands available, with the differences being primarily in the construction and attention to details (see resources).
Rear Wheel Rollers
Rear-wheel chock stands provide support via a stand onto which you roll the bike. Their design has an angle stand that the bike rolls up onto, and an inverted middle with rollers that keep the wheel turning until you stop it. Then, the bike sits comfortably in the stand. These stands (see resources) offer the same benefits as the other two types of chocks, primarily the ability to either park the bike or perform maintenance.
Friday, April 4, 2014
How to Test the Wheel Sensor on a 2001 Chevrolet Silverado
2001 Chevrolet Silverados use a hub-mounted wheel sensor system that consists of an electro-magnetic sensor and a notched reluctor wheel on each front wheel. The reluctor wheel spins at the same RPM as the wheel and the electro-magnetic sensor records this information in pulses. The PCM and ABS computers decode this information and use it determine wheel speed. By determining the wheel speed, both computers can tell if a wheel is locked up or spinning faster than the other. In order to diagnose a faulty wheel sensor, you must monitor the data stream with a scan tool and also confirm that each sensor is receiving voltage.
Instructions
- 1
Lift the front portion of vehicle with a jack and support it with jack stands; both front tires must be at least 6-inches off of the ground. Place wheel chocks behind the rear wheels and apply the parking brake.
2Switch the ignition to the ON position and connect a scan tool to the trucks data port under the dashboard below the steering wheel. Navigate to the live data menu and monitor the wheel speed sensors; they should both read zero.
3Turn on the engine and lightly depress the throttle while monitoring the scan tool. The wheel speed sensor output readings should match the speedometer output. If one sensor does not then it is most likely faulty.
4Turn off the engine but leave the ignition on and lie down on a mechanics creeper. Roll underneath the car and examine the wheel speed sensor wires for fraying or cuts.
5Unplug the connector from the wheel speed sensor. Probe the light blue wire for the left-front wheel sensor and the tan wire for the right-front wheel sensor with a digital multimeter. The specified voltage value is 1.8 to 12 volts. If the multimeter reads less than 1.8 volts then find and repair the short in the wire and retest the sensor. If the voltage reading is within specification then replace the wheel speed sensor.